AGC Edge Lean Construction Education Units 1 – 5
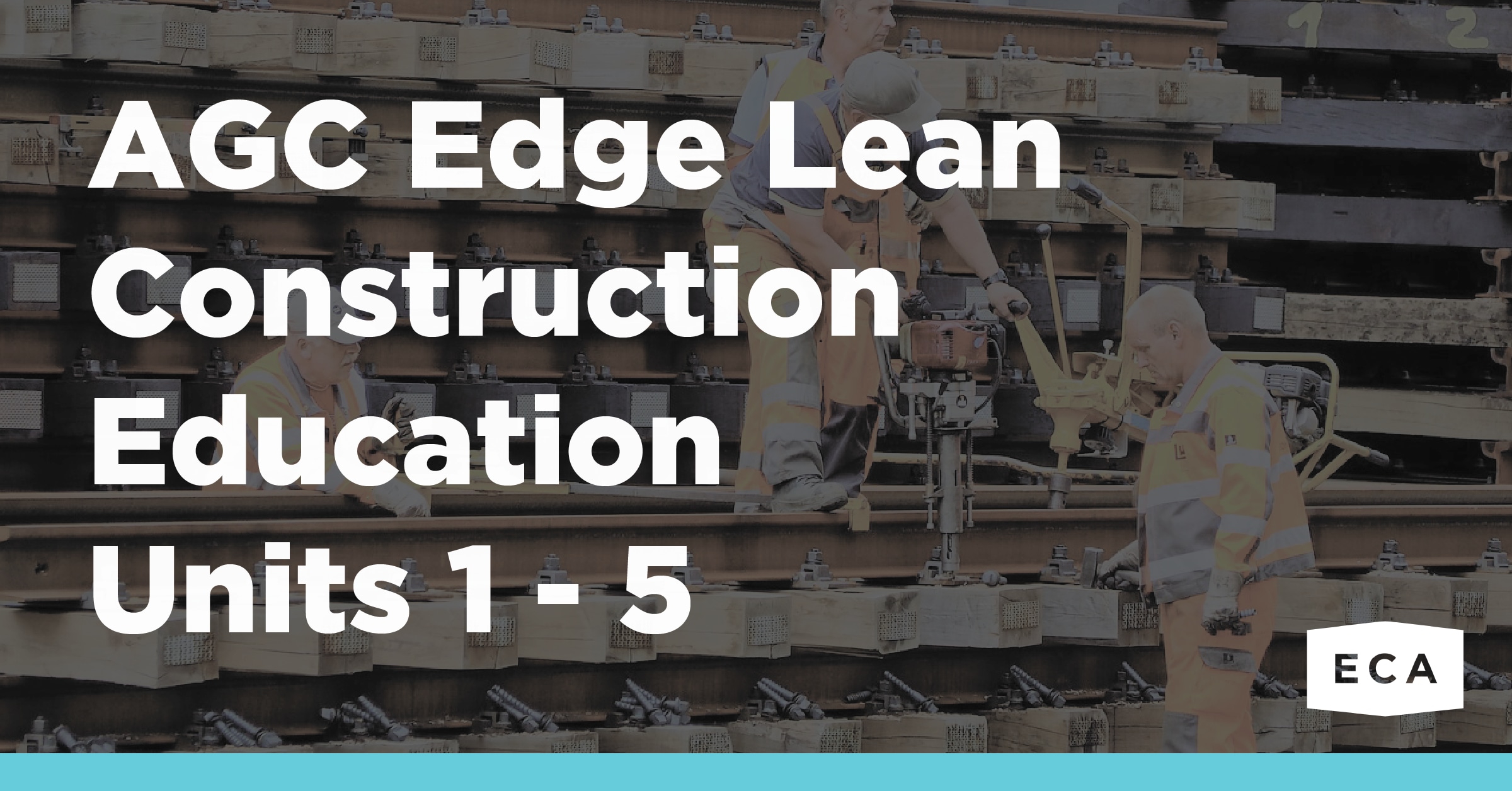
AGC Edge Lean Construction Education Units 1 – 5
January 14, 2025 8:30 AM - January 22, 2025 4:30 PM (MST)
Description
LEAN CONSTRUCTION EDUCATION PROGRAM – SECOND EDITION
Lean Construction is driven to minimize costs and maximize value on each project completed, challenging all stakeholders to develop and apply better ways to manage the overall construction process.
The updated AGC Lean Construction Education Program engages students with numerous activities and group discussions designed to apply Lean Construction principles and practices. Key course activities include the Parade of Trades exercise where participants will learn the effects of varying and unreliable workflow versus smooth and reliable workflow. Students will also learn and practice the Last Planner® System in a simulation that teaches students to engage in a way that produces predictable workflow and rapid learning. After participants complete all five units in the program, they become eligible to sit for an exam to earn the Certificate of Management – Lean Construction (CM-Lean).
Delivery Model
All sessions are conducted virtually using the Zoom platform
LEAN CONSTRUCTION EDUCATION PROGRAM MODULES
Unit 1: Introduction to Lean Construction
- Lesson 1 – Why Lean?
- Lesson 2 – What is Lean & Respect for People Objectives
The first two lessons answer the questions Why Lean? and What is Lean? Then it introduces participants to the six tenets of Lean Construction and explains how Respect for People is a fundamental goal of Lean as we work to develop people and make work an enriching experience.
- Lesson 3 – Generate Value, Remove Waste, & Optimize the Whole
Explains the way value is defined by the customer, and that each customer will define value differently. Instructors illustrate that non-value-adding activities are pure waste. Lean uses the principle of prioritizing flow efficiency as a key means to generate value and remove waste.
- Lesson 4 – Continuous Improvement
Defines continuous improvement and provides an understanding of how Plan-Do-Check-Act, PDCA, supports continuous improvement. Participants will practice PDCA in a group exercise.
Unit 2: Process and Production Basics
- Lesson 1 - Process, Efficiency & Variation
Provides a description of what a process and process flow are, then describes what makes a process efficient. From there instructors define what variation, what it looks like in our work, and what causes it, so in the next lesson we can see how variation impacts a process, its flow, and its efficiency and what that means for our projects.
- Lesson 2 - Law of Variation
Explains how variation, buffers, and consistency affect project performance, and identify the characteristics and consequences of unreliable workflow and reliable workflow. Participants will learn these lessons firsthand in the Parade of Trades simulation.
- Lesson 3 - Variation Mitigation
Describes buffers, buffer sizing and other means to mitigate variation. Participants learn specific techniques for reducing variation, and the importance of process consistency.
- Lesson 4 - 5S
Shows how 5S is another Lean method to help reduce variation on projects, and it does much more. It is a means for pursuing continuous improvement. It helps us reduce waste. It shows respect for people by improving their work environment and contributing to a safer workplace.
Unit 3: Production Systems
- Lesson 1 - Lean Production Systems
The overall lesson objective is to introduce key terms and recognize aspects of common practice to create a Lean production system for construction that prioritizes flow efficiency.
- Lesson 2 - Batch-Pull-Balance-Takt Simulation
Participants experience the effects of batching, pull, balancing and takt on a production system by completing the Batch, Pull, Balance, Takt Exercise.
- Lesson 3 - Lean Production Systems – Pull
The focus is on Pull as part of the control for the system. Participants learn how pull helps manage variation and explain the impact of pull control on production systems.
- Lesson 4 - Lean Production Systems - Law of Bottlenecks & Balance, Little’s Law & Batching
The overall objective for this lesson is for participants to recognize the impact of batching on construction production and flow efficiency by looking at Little's Law and the risks and advantages of batching.
Unit 4: Lean Thinking Applied to Field Production, Last Planner System
- Lesson 1 - Introduction to Last Planner System® (LPS)
Describes how the LPS is a method of planning and control for the entire project. LPS is a common starting point for companies or projects embarking on a Lean journey. This lesson introduces LPS in terms of how it embodies the six tenets both in its design and goals in the context of field production.
- Lesson 2 - Details of the Last Planner System
Describes the ideal for running the full LPS. Participants will learn the different tools, visuals, and formats that are used, but their goal of each conversation is the same. This lesson shows the steps of the Last Planner System and how it gets more detailed the closer teams get to the work. As the lesson progresses participants see the purpose of each level of the LPS, and how the levels of the LPS work together. Participants will identify methods to encourage trade partner participation in each level of the LPS, and measure to see if processes are being followed and achieving the desired results.
Unit 5: Lean Thinking Outside of Field Production
- Lesson 1 - Lean Project Delivery
Describes how Lean is applied to the whole project delivery system. It explains the purpose and recognizes the advantages of cross-functional teams, and why value should be defined early in the project life cycle.
- Lesson 2 - Lean in the Supply Chain
Looks at improvements that can be made exclusively within the supply chain with an understanding of customer value but without involving changes by design or construction.
- Lesson 3 - Lean in Design
Describes how value creation in design focuses on identifying and meeting customer needs through efficient and effective design processes.
- Lesson 4 - Process Improvement & Problem Solving
Explains how effective problem solving is focused on proactively preventing the same type of problem from occurring again because it addresses root causes. It creates a culture of problem solving where everyone brings problems forward and collaboratively works to resolve them. Following the completion of all five units, participants will have the opportunity to pursue the AGC designation CM-Lean (Certificate of Management – Lean Construction) by writing the CMLean exam.
WORKSHOP INSTRUCTOR BIOGRAPHY
James Johnston, P. Eng., CM-Lean is an Industrial Engineer and the principal of Quality Dynamics Inc., a consulting & training organization focused on construction performance improvement. James is a Lean Construction project coach, an Approved Trainer with the Associated General Contractors of America and one of the core developers of the internationally recognized, industry standard Lean Construction Education Program. He is a construction, operations and quality specialist with over 30 years of experience focusing on delivering highly productive projects, business process analysis & improvement, Lean implementation, strategic planning and business development. He has worked extensively as a Management Consultant & Educator, leading organizations through lean transformations, quality system implementation and process optimization projects. He has coached & facilitated the implementation of Lean Construction tools and methodologies on projects of all sizes, has trained thousands of construction professionals internationally and continues to develop programs that improve project outcomes industry wide.
Construction Project Management
Estimating